Técnicas de Fabricación de Maletas: Moldeo por Vacío vs Moldeo por Inyección
Tabla de Contenidos
- Cómo Elegir el Proceso Adecuado para su Proyecto
- Proceso de Moldeo por Vacío
- Proceso de Moldeo por Inyección
- Comparación de Sostenibilidad
1. Cómo Elegir el Proceso Adecuado para su Proyecto
Moldeo por Vacío:
- Utilizado para piezas de plástico grandes y sencillas con menores necesidades de precisión.
- Optimiza volúmenes de producción medios y rentabilidad.
- Lo mejor para pedidos de bajo presupuesto y pequeñas cantidades con plazos ajustados.
Moldeo por Inyección:
- Elección para piezas de plástico complejas de gran volumen que requieren alta precisión y consistencia.
- Ideal para la producción a gran escala con una mayor inversión inicial pero menores costes por unidad a lo largo del tiempo.
2. Proceso de Moldeo por Vacío
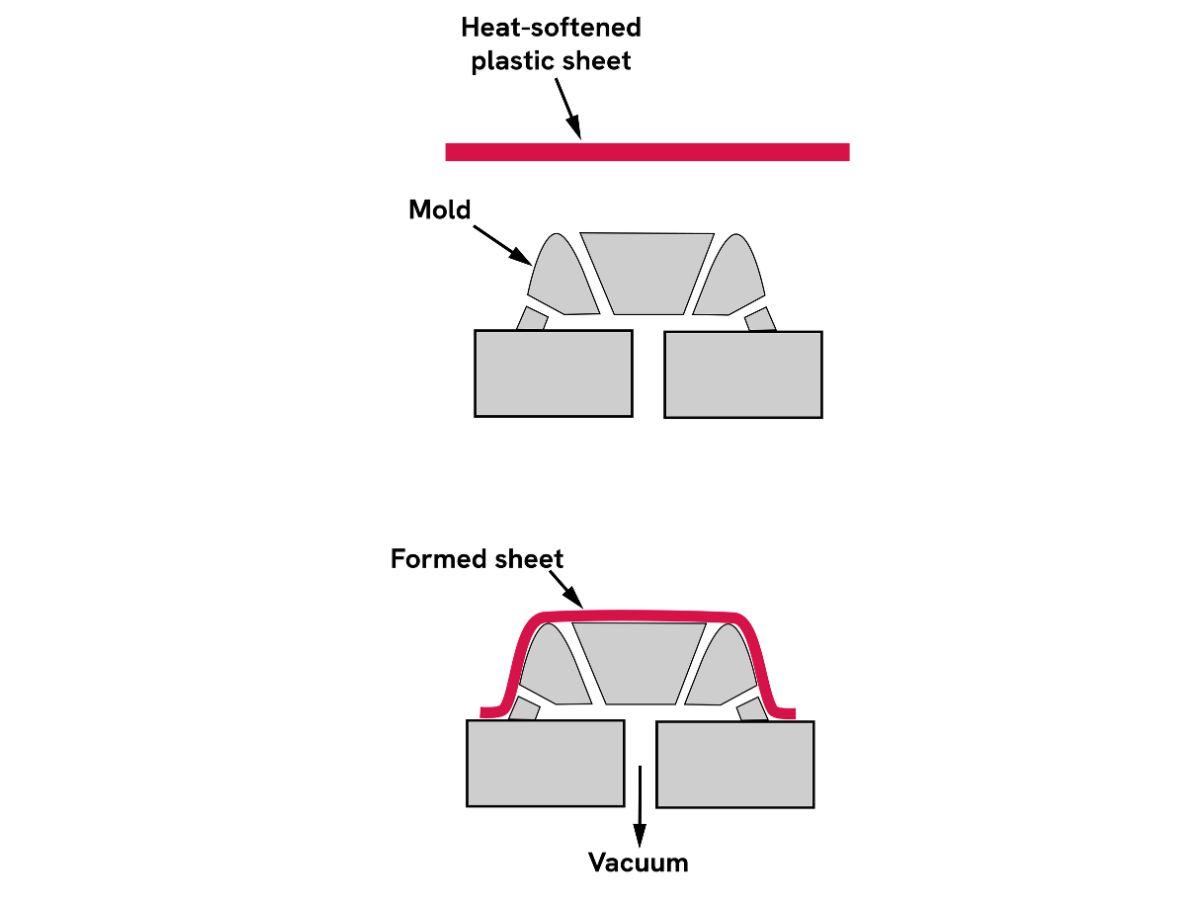
El moldeo por vacío da forma a láminas de plástico en intrincados diseños aplicando calor y presión al vacío. Este proceso de fabricación ofrece durabilidad y componentes ligeros, por lo que es una opción popular en la producción de equipaje.
Materiales Utilizados:
Pasos:
- Fijación de la Lámina: Fija una lámina de plástico utilizando un marco de sujeción.
- Calienta la Lámina: Utiliza controles de temperatura precisos para calentar la lámina de plástico sujeta con abrazaderas hasta que se ablande y se vuelva flexible.
- Posicionamiento sobre el molde: Coloca la lámina blanda sobre un molde prediseñado para darle la forma deseada.
- Activar el Vacío: Utiliza una bomba de vacío para apretar el plástico calentado contra el molde y capturar cada detalle.
- Enfriar la Lámina Formada: Dejar enfriar la lámina aún en el molde, manteniendo su nueva forma.
- Recortar el Material sobrante: Recorta el material sobrante una vez que la plancha se haya enfriado y endurecido, con lo que obtendrá el producto final.
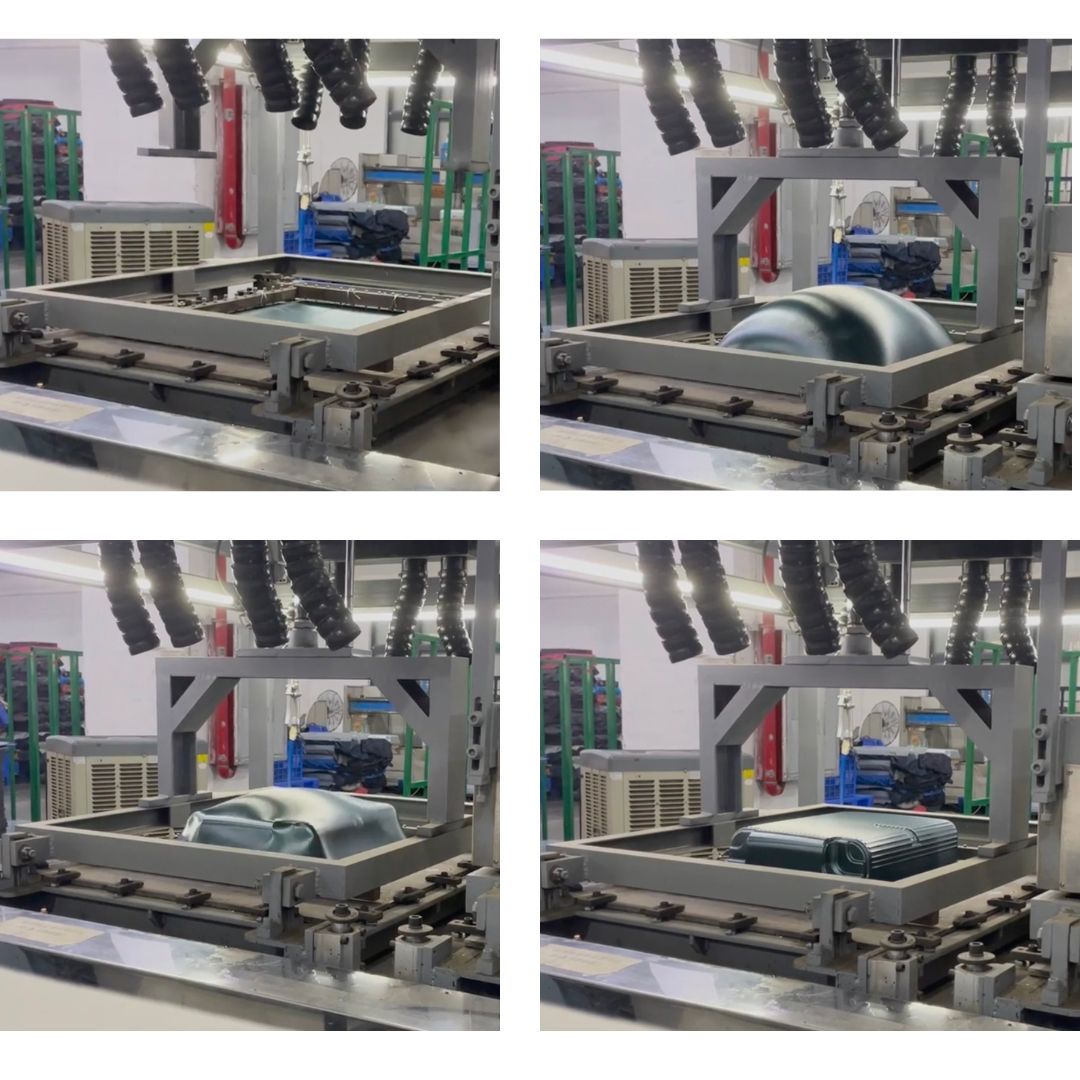
Ventajas:
- Rentabilidad: Relativamente barato en comparación con otros procesos de moldeo, lo que lo hace ideal para grandes series de producción.
- Durabilidad y ligereza: Materiales como el ABS y el PC proporcionan una estructura resistente pero ligera.
- Flexibilidad de Diseño: Permite diseños intrincados y personalización, lo que hace posible fabricar productos únicos conformados al vacío.
Aplicaciones:
- Maletas de Carcasa Rígida: Crea revestimientos exteriores duraderos con paredes de grosor y resistencia uniformes.
- Diseños personalizados y de edición limitada: Produce fácilmente formas y patrones únicos para colecciones personalizadas o especiales.
- Componentes Internos y Bandejas: Fabrica compartimentos, separadores y bandejas para organizar y proteger sus pertenencias.
3. Proceso de Moldeo por Inyección
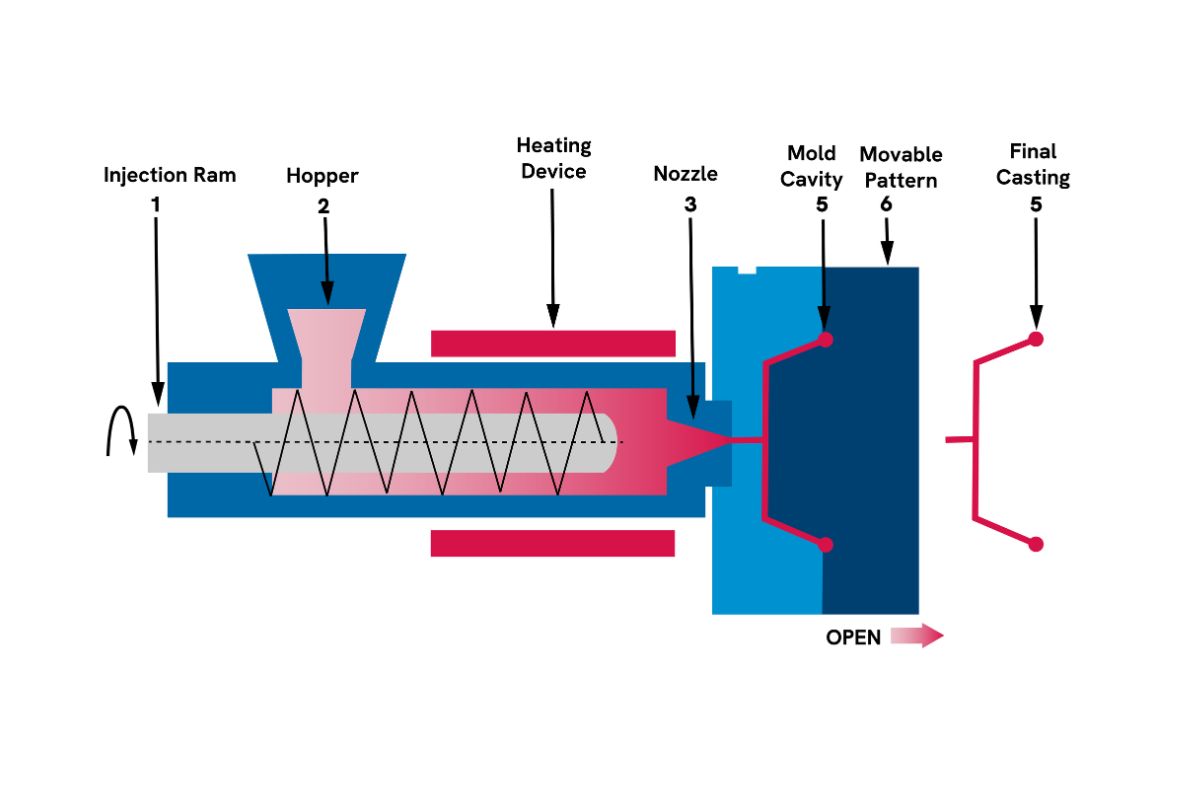
El moldeo por inyección produce eficazmente diversos componentes de equipaje con gran precisión y durabilidad. Este proceso de moldeo funciona bien para crear geometrías complejas y garantizar la producción de grandes volúmenes.
Materiales Utilizados:
- PP
- ABS
- PC
- Aluminio para componentes específicos como asas, cantoneras y ruedas.
Pasos:
- Fijar: Cierra firmemente el molde, que consta de dos mitades, garantizando ángulos de desmoldeo adecuados para facilitar el desmoldeo de las piezas.
- Inyectar: Calienta e inyecta gránulos de plástico en la cavidad del molde utilizando una máquina de moldeo por inyección, asegurándose de que el plástico llena todas las cavidades.
- Presurizar: Aplicar presión adicional para asegurarse de que la cavidad del molde se llena completamente y el material plástico se ajusta a la forma del molde.
- Enfriar: Dejar que el plástico se enfríe y se endurezca en la forma del molde con canales de refrigeración.
- Abrir: Separar el molde para liberar la pieza formada.
- Expulsar: Utilizar clavijas expulsoras para empujar la pieza fundida final fuera de la cavidad.
Ventajas:
- Alta eficiencia: Ideal para la producción en serie, permitiendo que un mismo molde produzca numerosas piezas.
- Precisión y Coherencia: Garantiza una alta precisión y una calidad constante en las piezas fabricadas.
- Rentable: Menor coste por pieza en la producción a gran escala, lo que lo convierte en un proceso eficaz para necesidades de gran volumen.
- Versatilidad del Material: Utiliza una amplia gama de termoplásticos en función de las propiedades deseadas de los componentes del equipaje.
Aplicaciones:
- Asas y Ruedas: Produce componentes duraderos y de alta precisión.
- Componentes Estructurales Internos: Garantiza piezas resistentes y ligeras que mantengan la integridad del equipaje.
- Mecanismos de Cerradura y Cremallera: Crea componentes intrincados para cierres.
4. Comparación de Sostenibilidad: Moldeo por Vacío vs. Moldeo por Inyección
¿Qué es más sostenible?
Tiradas de Producción Pequeñas y Medianas:
- Moldeo por Vacío: Ofrece más sostenibilidad gracias a un menor consumo de energía y a unos tiempos de preparación de la producción más rápidos. El tiempo necesario para configurar las máquinas de conformado al vacío es menor, por lo que resulta ideal para tiradas más pequeñas.
Producción a Gran Escala:
- Moldeo por Inyección: Proporciona más sostenibilidad gracias al uso eficiente del material y a los residuos mínimos. La producción de grandes volúmenes en el moldeo por inyección puede compensar los costes energéticos iniciales.
Eficiencia del Material:
- Moldeo por Vacío: Utiliza láminas de plástico, lo que supone un cierto desperdicio de material durante el recorte. El material sobrante puede reciclarse, aunque es menos eficaz que el moldeo por inyección.
- Moldeo por Inyección: Utiliza granzas de plástico con un mínimo de residuos. Redondea y reutiliza materiales, generando menos residuos y mejorando su eficiencia.
Consumo de Energía:
- Moldeo por Vacío: Consume menos energía por pieza, ideal para tiradas pequeñas y medianas. Los tiempos de preparación y de ciclo más rápidos reducen el consumo total de energía.
- Moldeo por Inyección: Requiere más energía debido al equipo de alta presión. Sin embargo, la eficiencia de la máquina de moldeo por inyección en la producción de grandes volúmenes compensa estos costes.
Generación de Residuos:
- Moldeo por Vacío: Genera residuos de bordes recortados y recortes. El reciclaje varía en función del material y de las capacidades locales, pero las máquinas de conformado al vacío pueden reciclar los residuos.
- Moldeo por Inyección: Produce un mínimo de residuos gracias a los precisos procesos de inyección. La alta reciclabilidad de los residuos plásticos aumenta aún más la sostenibilidad.
Impacto Medioambiental:
- Moldeo por Vacío: Menor huella de carbono para tiradas pequeñas y medianas. Mejora la sostenibilidad utilizando hojas recicladas y una gestión eficaz de los residuos.
- Moldeo por Inyección: Huella de carbono inicial más alta, pero eficiente para la producción a gran escala. Utiliza maquinaria energéticamente eficiente y plásticos biodegradables/reciclados para reducir el impacto.
A la hora de decidir cuál es la mejor técnica de fabricación de maletas para su marca, es fundamental adoptar un enfoque práctico. Visite las fábricas para ver los procesos y reunirse con los propietarios. Cada fábrica tendrá prácticas únicas que pueden influir en sus resultados, como el pulido de los exteriores y la gestión de los problemas. La gestión de estos factores es tan importante como el propio proceso de fabricación. No dude en ponerse siempre en contacto con el equipo de Travel Sentry para obtener apoyo y orientación.
Moldeo por Vacío:
Utilícela para piezas de plástico grandes y sencillas con menores necesidades de precisión.
Optimizada para volúmenes de producción medios y rentabilidad.
Lo mejor para pedidos de bajo presupuesto y pequeñas cantidades con plazos ajustados.
Moldeo por Inyección:
Elección para piezas de plástico complejas y de gran volumen que requieren alta precisión y consistencia.
Ideal para la producción a gran escala con una mayor inversión inicial pero menores costes por unidad a lo largo del tiempo.
Si tiene en cuenta estas recomendaciones y evalúa a fondo sus necesidades de producción, podrá tomar una decisión informada que se ajuste a los objetivos de su marca y garantice una fabricación de equipaje de alta calidad.
Vea la guía de materiales aquí