Luggage Manufacturing Techniques: Vacuum Forming vs Injection Molding
Table of Contents
- How to Choose the Right Process
- Vacuum Forming Process
- Injection Molding Process
- Sustainability Comparison
1. How to Choose the Right Process for Your Project
Vacuum Forming:
- Use for large, simple plastic parts with lower precision needs.
- Optimize for medium production volumes and cost-effectiveness.
- Best for low-budget, small-quantity orders with tight schedules.
Injection Molding:
- Choose for high-volume, complex plastic parts requiring high precision and consistency.
- Ideal for large-scale production with higher initial investment but lower per-unit costs over time.
2. Vacuum Forming Process
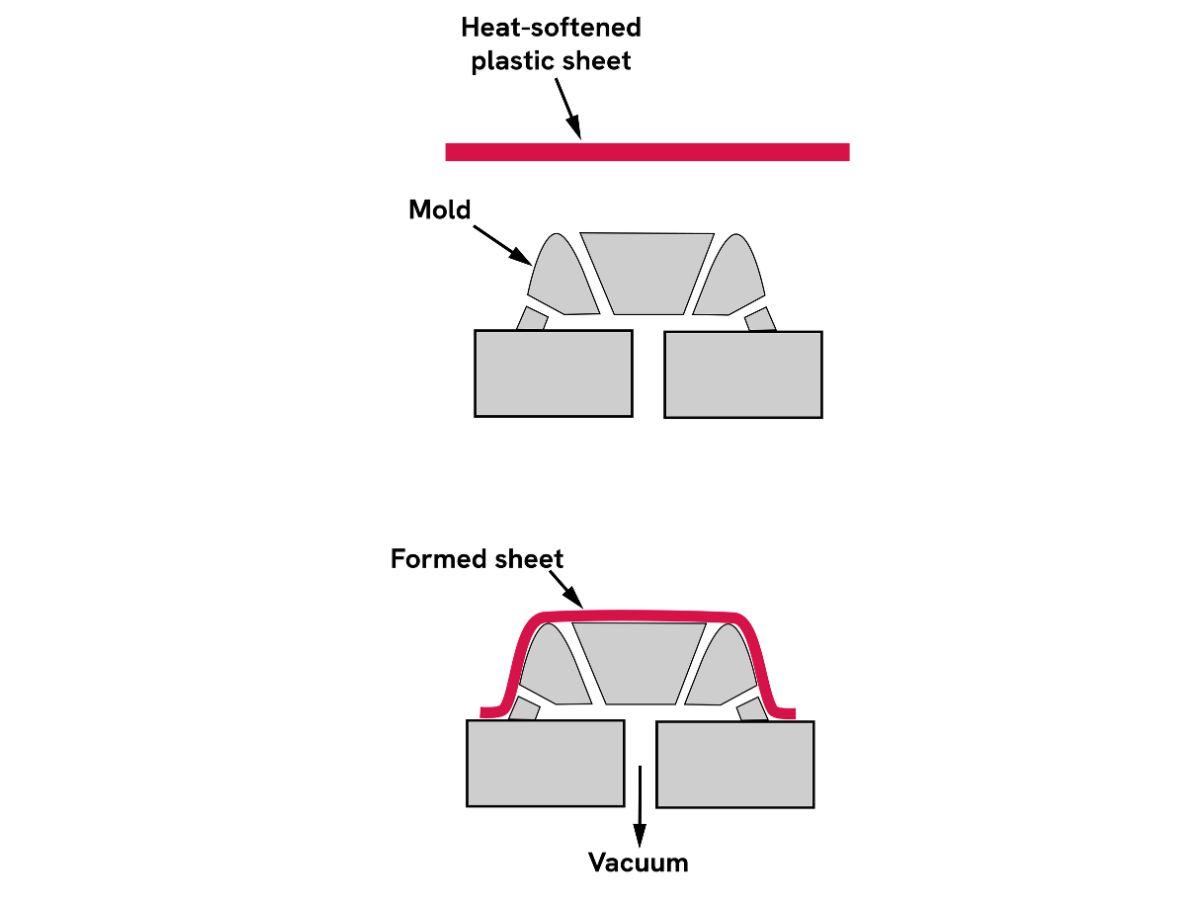
Vacuum forming effectively shapes sheets of plastic into intricate designs by applying heat and vacuum pressure. This manufacturing process offers durability and lightweight components, making it a popular choice in luggage production.
Materials Used:
See our luggage materials guide here.
Steps:
- Clamp the Sheet: Secure a plastic sheet using a clamping frame.
- Heat the Sheet: Use precise temperature controls to heat the clamped plastic sheet until it becomes soft and pliable.
- Position Over the Mold: Place the soft sheet over a pre-designed mold to form the desired shape.
- Activate the Vacuum: Utilize a vacuum pump to pull the heated plastic tightly against the mold and capture each detail.
- Cool the Formed Sheet: Allow the sheet to cool while still on the mold, maintaining its new form.
- Trim Excess Material: Trim any excess material once the sheet has cooled and hardened, resulting in the final product.
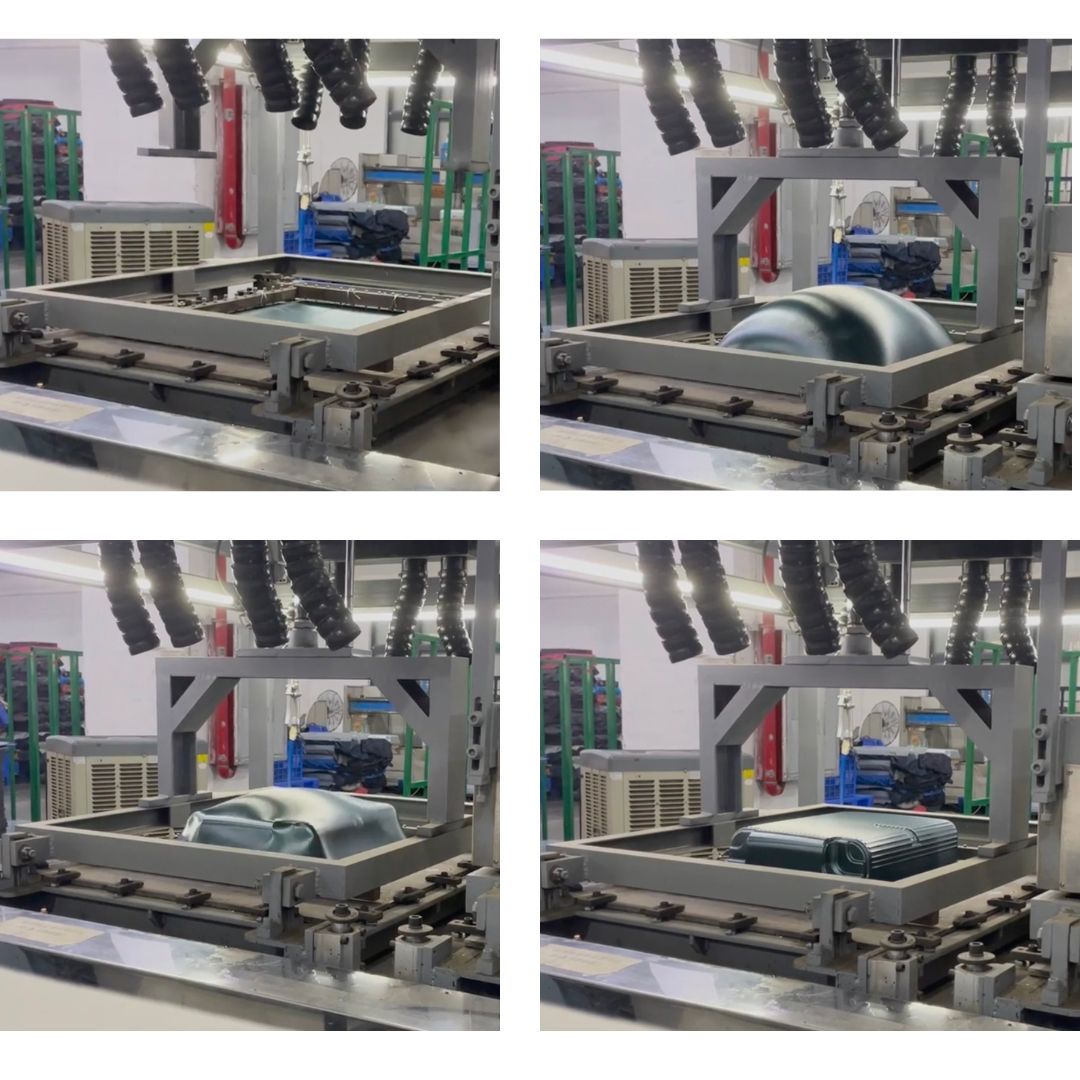
Advantages:
- Cost-Effectiveness: Relatively inexpensive compared to other molding processes, making it ideal for large production runs.
- Durability and Lightweight: Materials like ABS and PC provide a strong yet lightweight structure.
- Design Flexibility: Allows intricate designs and customization, making it possible to produce unique vacuum-formed products.
Applications:
- Hard-Shell Luggage Shells: Create durable outer shells with consistent wall thickness and strength.
- Custom and Limited-Edition Designs: Easily produce unique shapes and patterns for personalized or special collections.
- Internal Components and Trays: Manufacture compartments, dividers, and trays to organize and protect belongings.
3. Injection Molding Process
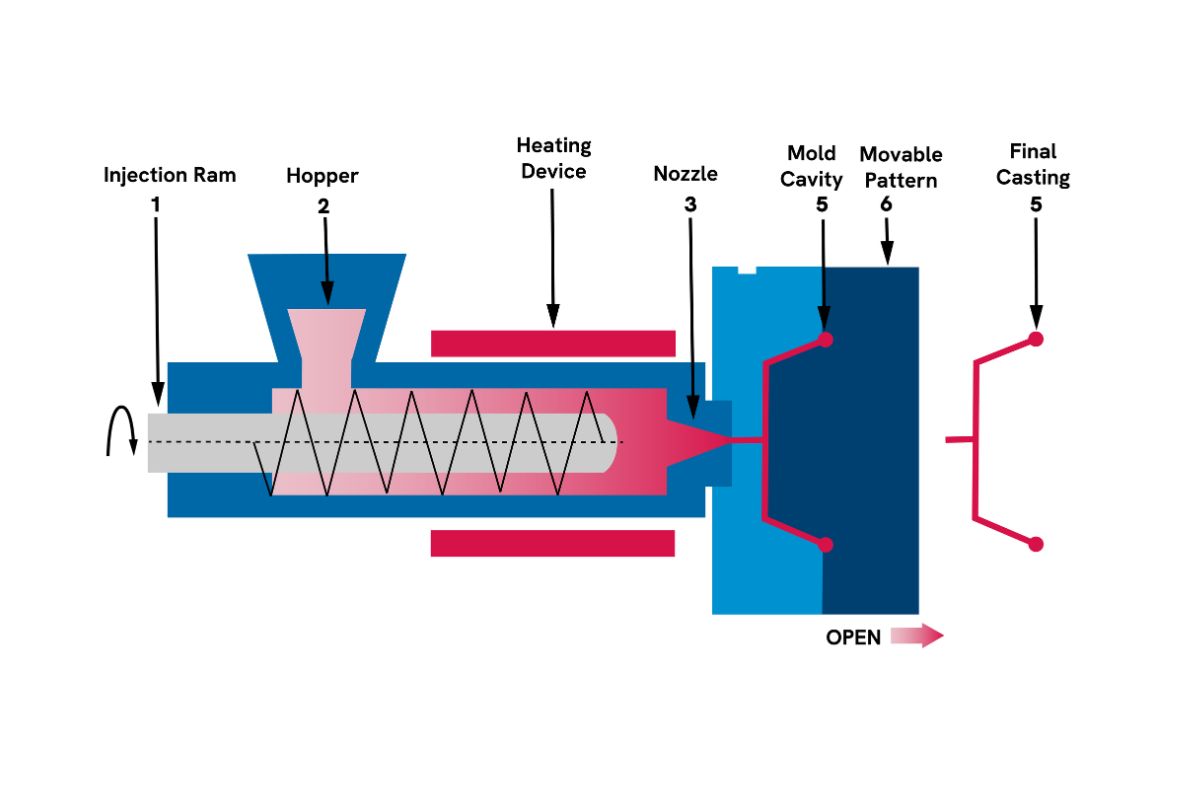
Injection molding efficiently produces various luggage components with high precision and durability. This molding process works well for creating complex geometries and ensuring high-volume production.
Materials Used:
- PP
- ABS
- PC
- Aluminum for specific components like handles, corner protectors, and wheels.
Steps:
- Clamp: Securely close the mold, which consists of two halves, ensuring appropriate draft angles for easy part release.
- Inject: Heat and inject plastic pellets into the mold cavity using an injection molding machine, ensuring the plastic fills every cavity.
- Pressurize: Apply additional pressure to ensure the mold cavity fills completely and the plastic material conforms to the mold's shape.
- Cool: Allow the plastic to cool and harden into the mold's shape with cooling channels.
- Open: Separate the mold to release the formed part.
- Eject: Use ejector pins to push the final casting out of the cavity.
Advantages:
- High Efficiency: Ideal for mass production, allowing the same mold to produce numerous parts.
- Precision and Consistency: Ensures high accuracy and consistent quality in the manufactured parts.
- Cost-Effective: Lower per-part cost in large-scale production, making it an efficient process for high-volume needs.
- Material Versatility: Use a wide range of thermoplastics based on the desired properties of the luggage components.
Applications:
- Handles and Wheels: Produce durable and high-precision components.
- Internal Structural Components: Ensure strong and lightweight parts that maintain luggage integrity.
- Zipper and Lock Mechanisms: Create intricate components for closures.
4. Sustainability Comparison: Vacuum Forming vs. Injection Molding
Which is More Sustainable?
Small to Medium Production Runs:
- Vacuum Forming: Offers more sustainability because of lower energy consumption and faster production setup times. The time required to set up vacuum forming machines is shorter, making it ideal for smaller runs.
Large-Scale Production:
- Injection Molding: Provides more sustainability because of efficient material usage and minimal waste. High-volume production in injection molding can offset initial energy costs.
Material Efficiency:
- Vacuum Forming: Uses plastic sheets, resulting in some material waste during trimming. Excess material can be recycled, though it is less efficient than injection molding.
- Injection Molding: Uses plastic pellets with minimal waste. Reground and reuse sprues and runners, generating less waste and improving material efficiency.
Energy Consumption:
- Vacuum Forming: Consumes less energy per part, ideal for small to medium runs. Faster setup and cycle times lower overall energy consumption.
- Injection Molding: This requires more energy because of the high-pressure equipment. However, the efficiency of the injection molding machine in high-volume production offsets these costs.
Waste Generation:
- Vacuum Forming: Generates waste from trimmed edges and offcuts. Recycling varies based on material and local capabilities, but vacuum forming machines can recycle the waste.
- Injection Molding: Produces minimal waste because of precise injection processes. The high recyclability of plastic waste further enhances sustainability.
Environmental Impact:
- Vacuum Forming: Lower carbon footprint for small to medium runs. Improve sustainability by using recycled sheets and efficient waste management.
- Injection Molding: Higher initial carbon footprint but efficient for large-scale production. Use energy-efficient machinery and biodegradable/recycled plastics to reduce impact.
When deciding on the best luggage manufacturing technique for your brand, it's crucial to take a hands-on approach. Visit the factories to see the processes and meet with the owners. Each factory will have unique practices that can impact your results, such as polishing exteriors and managing issues. The management of these factors is as important as the manufacturing process itself. Always feel free to contact the Travel Sentry team for support and guidance.
Vacuum Forming:
Use for large, simple plastic parts with lower precision needs.
Optimize for medium production volumes and cost-effectiveness.
Best for low-budget, small-quantity orders with tight schedules.
Injection Molding:
Choose for high-volume, complex plastic parts requiring high precision and consistency.
Ideal for large-scale production with higher initial investment but lower per-unit costs over time.
By considering these recommendations and thoroughly evaluating your production needs, you can make an informed decision that aligns with your brand's goals and ensures high-quality luggage manufacturing.