How Luggage is Made: Innovation in Machinery
Making a suitcase requires advanced machines and modern techniques. Each machine plays an important role in turning raw plastic into a finished product. These machines not only improve productivity but also save time and energy.
They are also part of a larger trend in manufacturing. Industries like construction use similar tools and processes.
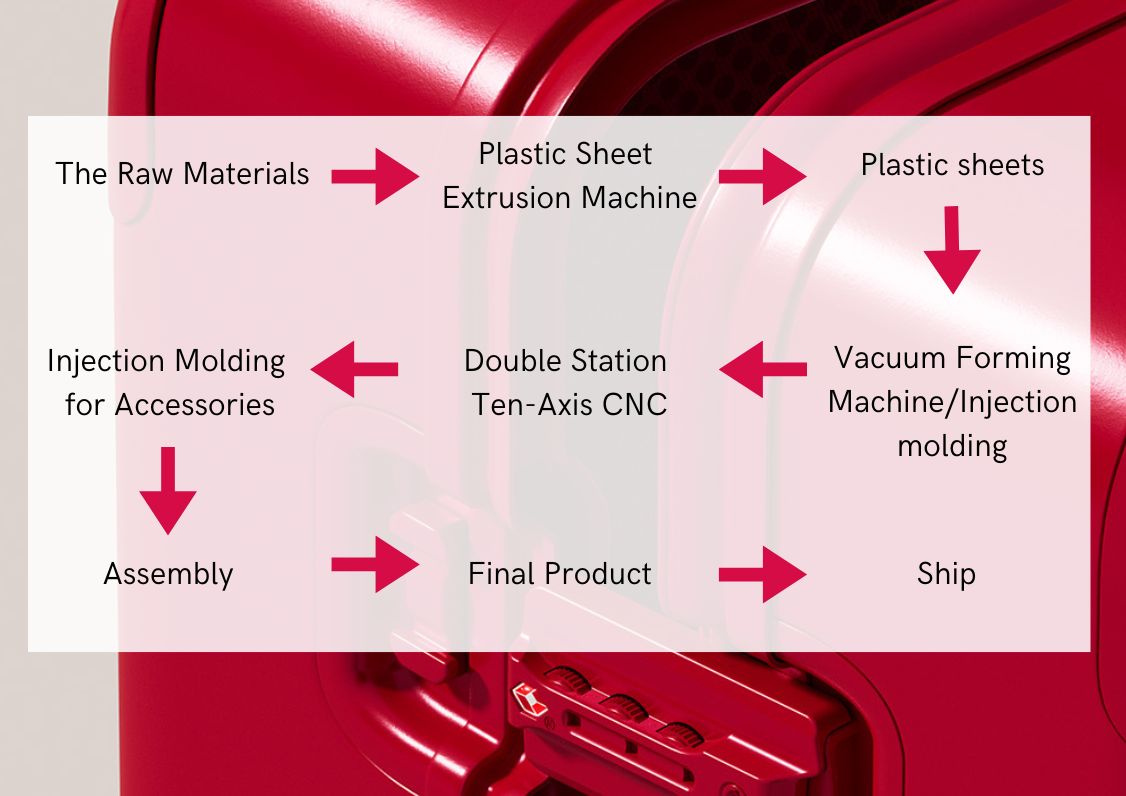
TABLE OF CONTENTS
- The Raw Materials
- Plastic Sheet Extrusion
- Creating the Shell
- Aluminum Molds
- Cutting and Punching - Double Station Ten-Axis CNC
- Injection Molding for Accessories
- Assembly
- Final Product
With the help of some of our licensees, here is a behind-the-scenes look at some exciting technologies shaping the luggage-making process.
1. The Raw Materials
What Happens: The process starts with the raw materials. These plastics include PC, ABS, RPET and PP, which are all popular when making luggage.
Using recycled plastic reduces waste and supports energy efficiency. Factories now use real-time data to check the quality of these raw materials, ensuring consistency.
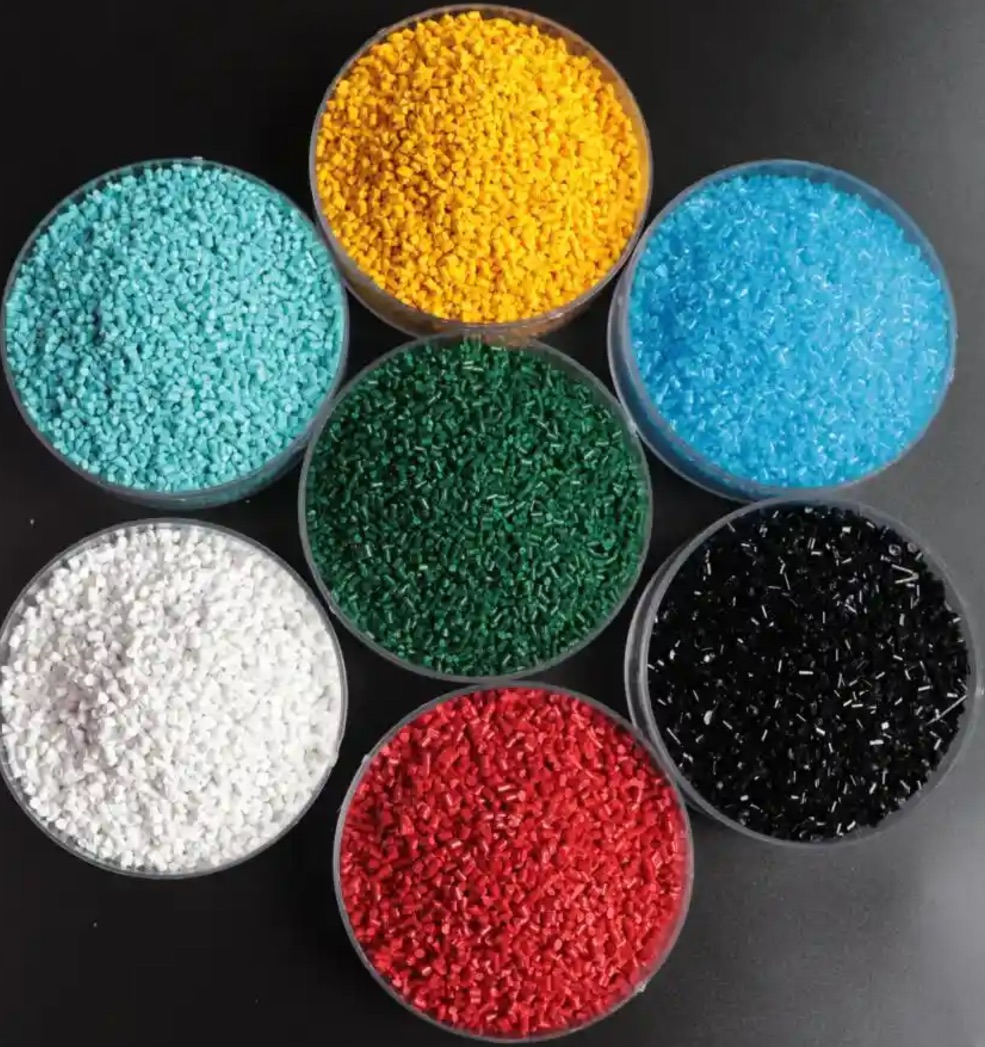
2. Plastic Sheet Extrusion
What Happens: Small plastic pellets are melted and turned into large flat sheets using a plastic sheet extruder machine.
How It Works:
- The machine heats and melts the pellets
- It presses the melted plastic into flat sheets of the required thickness and surface texture.
- The machine then cools and trims the sheets to size
- These sheets form the outer shell of the suitcase
Artificial intelligence (AI) monitors the process to ensure each sheet has the same thickness, improving quality.
When using RPET, due to the slightly higher thermal sensitivity of the material, the extruder machine needs a much longer cooling zone to make the sheets more stable for the next process, with AI ensuring consistent thickness and quality throughout. Machines shown here at Summit Luggage and Jiaxing Chuangying Travel Supplies Co., Ltd.
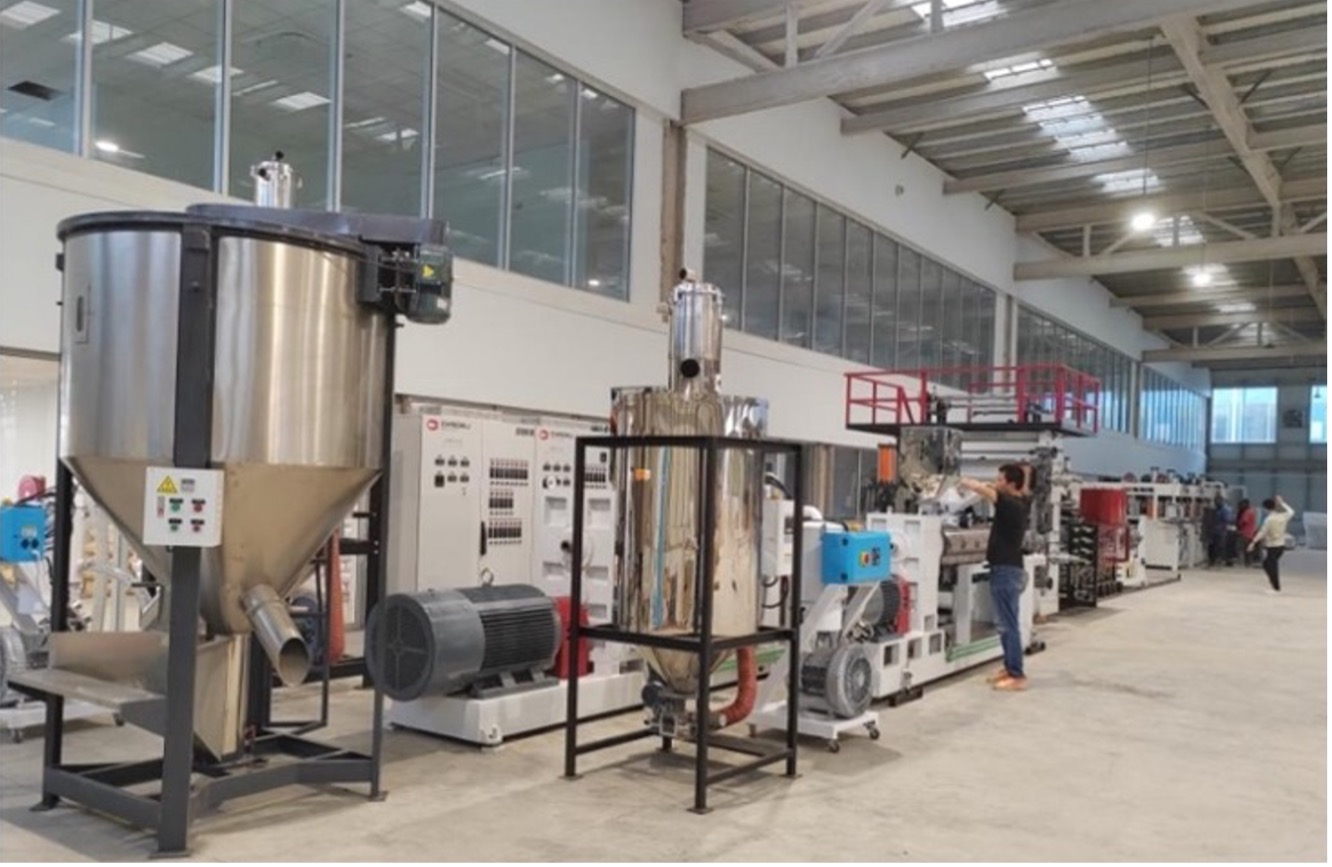
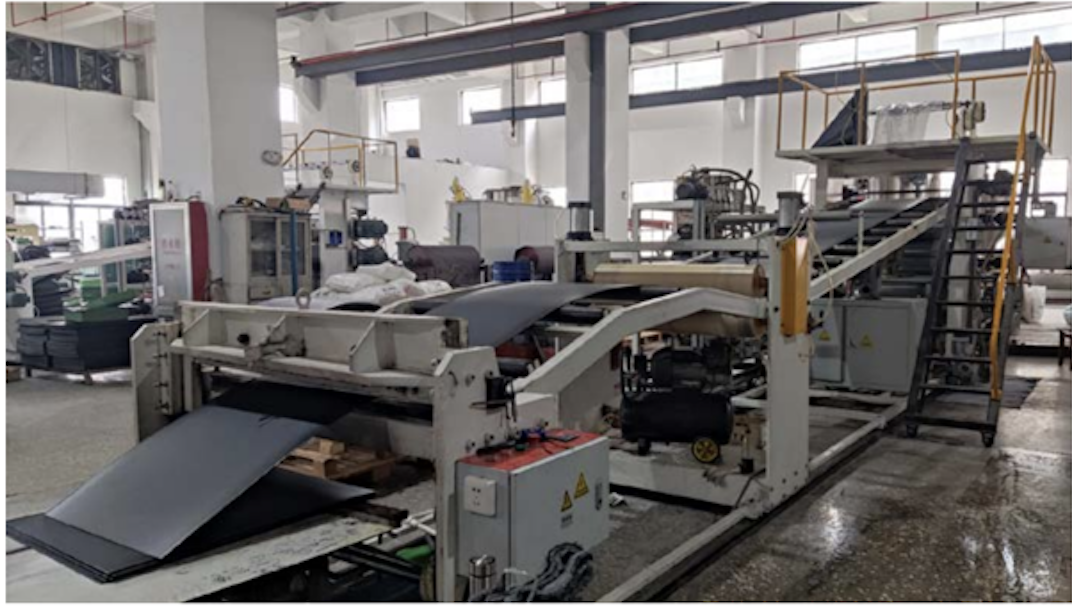
3. Creating the Shell of the Suitcase
Luggage shell manufacturing relies on two primary processes: vacuum forming and injection molding. These processes shape materials like ABS, PC, RPET and PP into durable and visually appealing suitcase shells.
Vacuum Forming:
Materials Used: PC and ABS are the most common materials for vacuum forming.
How It Works:
- Heating: The machine heats flat plastic sheets until they become soft and pliable.
- Forming: The heated sheet is placed over a custom aluminum mold.
- Vacuum Suction: A vacuum pulls the plastic tightly around the mold, shaping it into the front or back shell of the suitcase.
- Cooling: Fans or cooling systems solidify the plastic into the desired shape.
Advantages:
- Cost Efficiency: Lower mold costs make vacuum forming more economical for large-scale production.
- Design Flexibility: This process allows for intricate designs, vibrant colors, and printable surface patterns.
- Impact Resistance: PC/ABS sheets are tough and withstand heavy use, making them ideal for luggage shells.
Limitations:
- Material Waste: Vacuum forming produces 20%-30% material scraps, increasing costs and environmental impact.
- Lower Recyclability: PC, in particular, has limited recyclability compared to PP.

Injection Molding:
Materials Used: PP (Polypropylene) is the preferred material for injection molding.
How It Works:
- Melting: Plastic pellets (PP) are melted into a liquid state.
- Injection: The molten plastic is injected into a mold cavity under high pressure.
- Filling: The plastic fills the mold completely, taking its precise shape.
- Cooling: Cooling channels in the mold solidify the plastic into the desired form.
- Ejection: Once cooled, the machine ejects the formed part, such as a suitcase shell or accessory.
Advantages:
- Lightweight: PP’s low density creates lighter luggage, which appeals to travelers looking for easy-to-carry options.
- Eco-Friendliness: The process produces almost no scrap material, aligning with sustainability goals.
- High efficiency: The shells finished by injection molding could skip the process of “Cutting and Punching,” saving time and energy resources.
- Toughness: PP is highly durable, flexible, and resists cracking under pressure.
- Recyclability: PP’s recyclability makes it an environmentally friendly choice for luggage manufacturing.
Limitations:
- High Mold Costs: Injection molding requires expensive molds, making it less cost-effective for small production runs.
- Design Constraints: It lacks the flexibility of vacuum forming for producing custom or small-batch designs.
PP injection molding machinery at ITP Luggage Group:
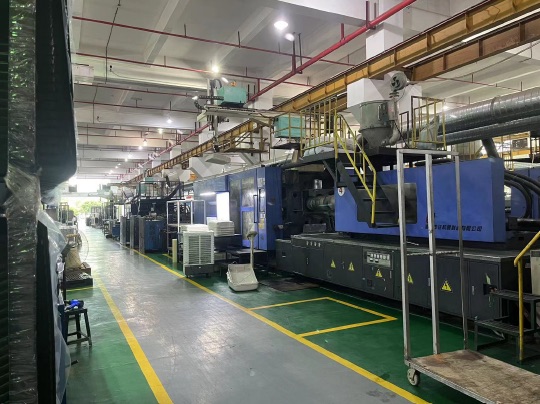
4. Aluminum Molds
The vacuum-forming machine uses aluminum molds to shape the plastic shells.
Aluminum molds are lightweight and cool quickly, saving time and energy. CNC machines make these molds with high precision, ensuring each suitcase looks perfect.
5. Cutting and Punching - Double Station Ten-Axis CNC
What Happens: The machine trims and cuts the formed suitcase shells to fit. It punches holes for handles, wheels, and locks.
How It Works:
- CNC cutting machines follow pre-set designs to trim the edges and cut holes.
- The machine punches holes accurately to attach handles, wheels, drawbars and TSA locks.
Heavy equipment like CNC machines, shown here at Wenzhou Chaoxu Machinery, ensures accurate cutting and punching. Real-time data helps machines adjust, reducing waste and errors.

6. Injection Molding for Accessories
What Happens: Small parts like wheels, handles, and feet are made using injection molding.
How It Works:
- Plastic is melted and injected into molds to form the parts.
- The molds cool and someone ejects the parts.
This method ensures the parts are strong and precise. Additive manufacturing (3D printing) is sometimes used to make prototypes or customized parts.
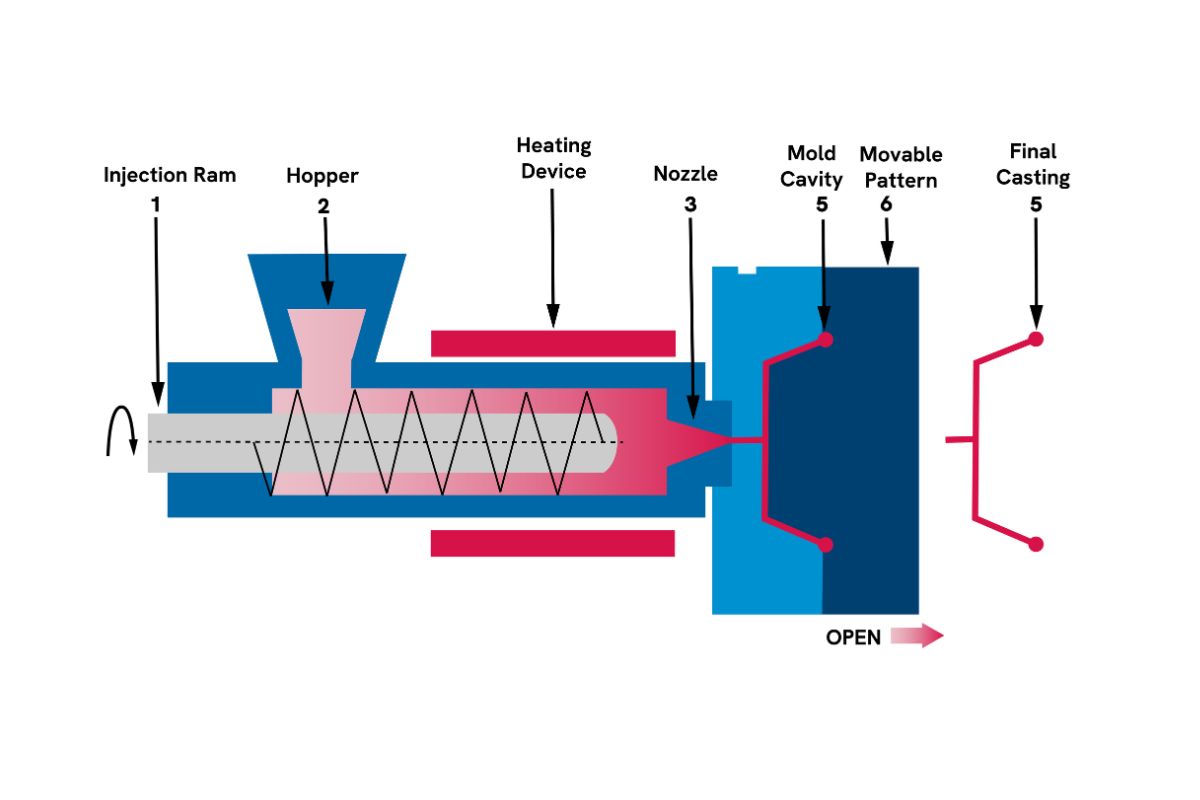
7. Assembly
What Happens: The trimmed shells are assembled with linings, zippers and other components.
How It Works:
- Sewing machines attach fabric linings and zippers to the shells.
- Factory workers install handles, wheels and TSA locks using rivets or screws.
- Some factories use robots to improve speed.
This step combines all the parts into a complete suitcase. Predictive maintenance ensures machines stay in top condition, avoiding delays. Assembly lines are shown here at Yangzhou Guohui and Summit Luggage.
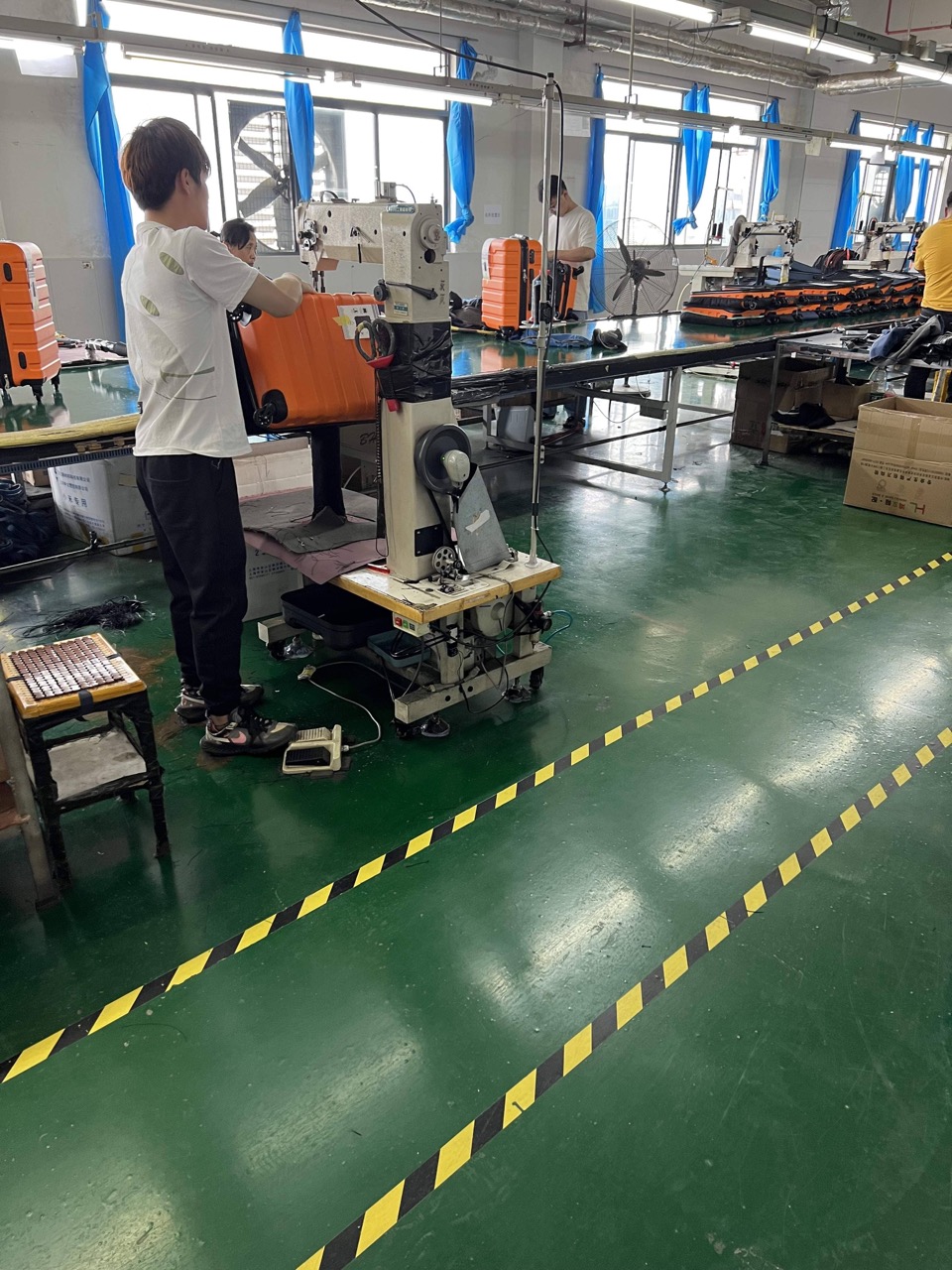
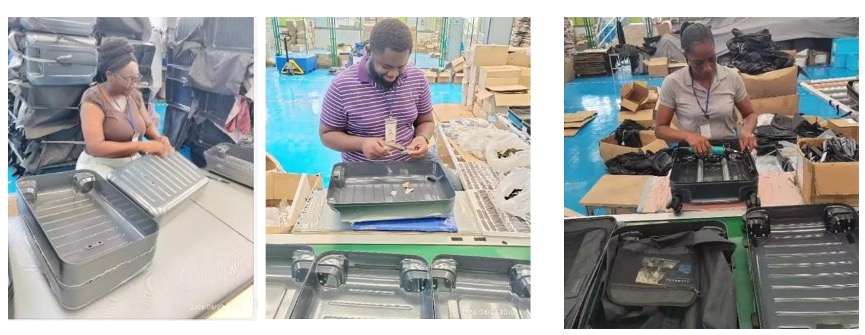
8. Final Product
What Happens: The finished suitcase goes through quality checks before being packaged and shipped.
How It Works:
- Inspectors check the suitcase for matching situation of front and rear shells, scratches, dents, or loose parts.
- If everything looks good, the suitcase will be packed for delivery.
Quality control ensures the customer gets a durable and well-made product. Factories use valuable insights from AI and real-time data to improve future production. Quality checks here at Shanghai JiYu Industry Co., Ltd:
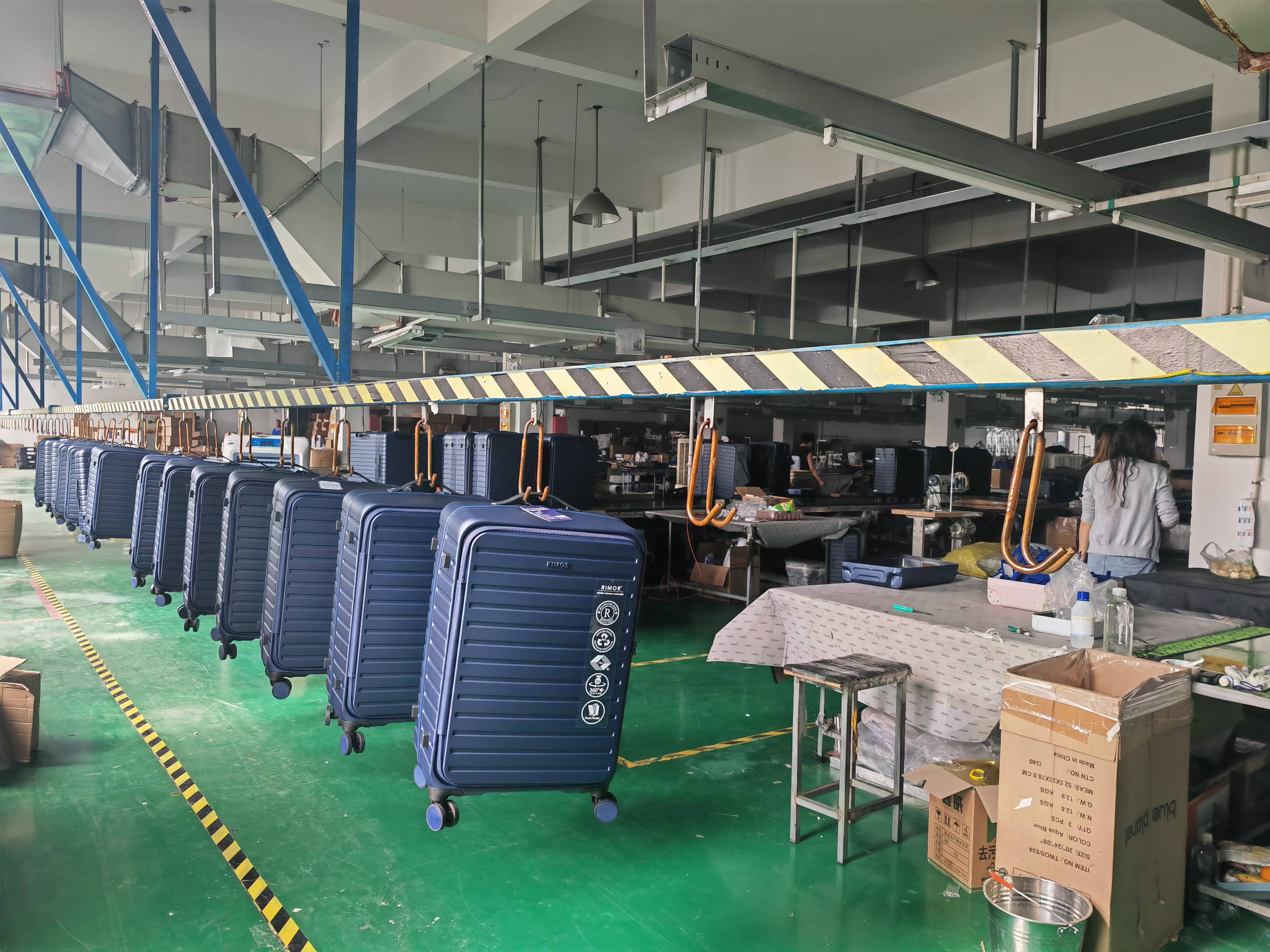
What Makes This Process So Innovative?
The machines used to make luggage are part of a larger trend in the manufacturing industry. Here’s how these innovations help:
- Improving Productivity: Machines like vacuum formers and CNC cutters increase speed and precision.
- Energy Efficiency: Modern machines use less power, reducing costs and environmental impact.
- Supply Chain Optimization: Factories track materials and avoid delays using real-time data.
- Long-Term Reliability: With predictive maintenance, factories keep their machines running smoothly.
- Cross-Industry Impact: These machines are not just for luggage. The construction business uses similar tools to make panels, parts and more.
Luggage manufacturing has come a long way in the last 20 years. With artificial intelligence, additive manufacturing, and real-time data, factories can make high-quality suitcases faster and more efficiently.